-
The SCOTT Addict SE was designed from the ground up with those longer days in mind. Featuring electronic shifting, carbon wheels and geometry that is less focused on racing and more on enduring, this bike is yearning to eat up some miles!
Please note that bike specifications are subject to change without prior notice.
condition of usage 6 -
Frame
Addict Disc HMF Carbon
Endurance geometry / Replaceable Derailleur Hanger
Internal cable routing
Syncros fender kit ready -
Fork
Addict HMF Disc
1 1/4"-1 1/2" Excentric Carbon steerer -
Rear Derailleur
Shimano Ultegra Di2 RD-R8150-SS
24 Speed Electronic Shift System -
Front Derailleur
Shimano Ultegra Di2 FD-R8150
Electronic Shift System
-
Shifters
Shimano Ultegra ST-R8170
24 Speed Electronic Shift System -
Crankset
Shimano Ultegra FC-R8100
Hollowtech II 50x34 T -
BB-Set
Shimano SM-BB72-41B -
Chain
Shimano CN-M6100-12 -
Cassette
Shimano CS-R7100
11-34 -
Brakes
Shimano BR-R8170 Hyd.Disc -
Rotor
Shimano SM-MT800 CL rotor 160/F and 160/R -
Handlebar
Syncros Creston 2.0 Compact
Alloy 31.8mm -
H'stem
Syncros RR2.0
1 1/4" / four Bolt 31.8mm -
Seatpost
Syncros Duncan 1.0
27.2/350mm -
Seat
Syncros Tofino Regular 2.0 Channel -
Headset
Acros AIF-1134 -
Wheelset
DT Swiss ERC1600 SPLINE 35mm Disc
24 Front / 24 Rear
Syncros Axle / Removable Lever with Tool -
Front Tire
Schwalbe ONE Fold
700x32C -
Rear Tire
Schwalbe ONE Fold
700x32C -
Approx weight in KG
8 -
Approx weight in LBS
17.64 -
Max. System Weight
120kg
The overall weight includes the bike, the rider, the equipment, and possible additional luggage.
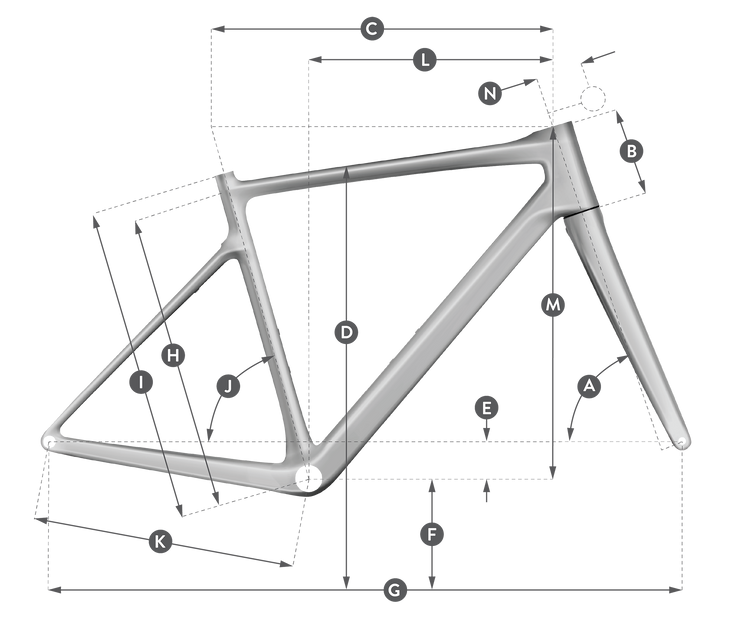
XXS/47 | XS/49 | S/52 | M/54 | L/56 | XL/58 | XXL/61 | |||||||||||
---|---|---|---|---|---|---|---|---|---|---|---|---|---|---|---|---|---|
A | head tube angle | 70.5 ° | 71.0 ° | 72.0 ° | 72.5 ° | 73.0 ° | 73.3 ° | 73.3 ° | |||||||||
B | head tube length | 95.0 mm | 105.0 mm | 125.0 mm | 145.0 mm | 165.0 mm | 185.0 mm | 205.0 mm | |||||||||
C | top tube horizontal | 515.0 mm | 525.0 mm | 540.0 mm | 555.0 mm | 570.0 mm | 585.0 mm | 600.0 mm | |||||||||
D | standover height | 732.0 mm | 747.0 mm | 775.0 mm | 790.0 mm | 812.0 mm | 835.0 mm | 848.0 mm | |||||||||
E | BB offset | -70.0 mm | -70.0 mm | -70.0 mm | -70.0 mm | -70.0 mm | -70.0 mm | -70.0 mm | |||||||||
F | BB height | 275.3 mm | 275.3 mm | 275.3 mm | 275.3 mm | 275.3 mm | 275.3 mm | 275.3 mm | |||||||||
G | wheel base | 996.7 mm | 1,003.0 mm | 1,005.0 mm | 1,010.6 mm | 1,015.4 mm | 1,022.8 mm | 1,036.5 mm | |||||||||
H | BB center to toptube center | 415.0 mm | 435.0 mm | 465.0 mm | 485.0 mm | 505.0 mm | 525.0 mm | 540.0 mm | |||||||||
I | BB center to top of seattube | 455.0 mm | 475.0 mm | 505.0 mm | 525.0 mm | 545.0 mm | 565.0 mm | 580.0 mm | |||||||||
J | seat angle | 75.0 ° | 75.0 ° | 74.5 ° | 74.0 ° | 73.5 ° | 73.1 ° | 73.0 ° | |||||||||
K | chainstay | 420.0 mm | 420.0 mm | 420.0 mm | 420.0 mm | 420.0 mm | 420.0 mm | 420.0 mm | |||||||||
L | reach | 376.3 mm | 383.2 mm | 387.0 mm | 390.9 mm | 394.3 mm | 398.6 mm | 406.6 mm | |||||||||
M | stack | 517.8 mm | 529.1 mm | 551.6 mm | 572.4 mm | 593.3 mm | 613.6 mm | 632.7 mm | |||||||||
N | stem length | 83.0 mm | 93.0 mm | 103.0 mm | 113.0 mm | 113.0 mm | 123.0 mm | 123.0 mm |